Hazardous Waste and Emergency Response Training Requirements:
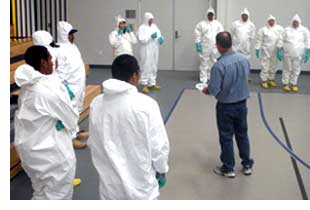
HAZWOPER is an acronym for the Hazardous Waste Operations and Emergency Response regulation mandated by Congress in 1986 (finalized in 1991), which required the Occupational Safety and Health Administration (OSHA) to come up with standards to train people who will clean up hazardous waste and materials.
All employees working on site that are exposed to hazardous substances, health hazards, or safety hazards and their supervisors and management responsible for the site shall receive training prior to engaging in hazardous waste operations. OSHA recognizes several levels of training and employees shall be trained to a level required by their job function and responsibility.
Each level requires a different training program, and OSHA specifies topics and minimum training times. The job descriptions and typical training time are detailed at www.osha.gov/law-regs.html. The overview provided here does not provide specific exemptions of a particular standards-related topic and does not itself alter or determine compliance responsibilities, which are set forth in OSHA standards themselves and the Occupational Safety and Health Act. Moreover, because interpretations and enforcement policy may change over time, for additional guidance on OSHA compliance requirements, the reader should consult current and administrative interpretations and decisions by the Occupational Safety and Health Review Commission and the Courts.
The HAZWOPER standard is categorized into various operations as outlined below (detailed in the sections below).
1)
Clean-up operations
that are conducted at uncontrolled hazardous waste sites, required by a governmental body, whether federal, state, local, or
other involving hazardous substances.
2)
Corrective actions
involving clean-up operations at sites covered by the Resource Conservation and Recovery Act of 1976 (RCRA).
3)
Voluntary clean-up
operations at sites recognized as uncontrolled hazardous waste sites by federal, state, local, or other governmental body.
4)
Operations involving
hazardous wastes that are conducted at treatment, storage, and disposal (TSD) facilities or by agencies under agreement with EPA to
implement RCRA regulations.
5)
Emergency response
operations for releases of, or substantial threats of releases of, hazardous substances without regard to the location of the hazard.

2)

3)

4)

5)

This includes any employees who are exposed or potentially exposed to hazardous substances, including hazardous waste, and who are engaged in one of the following operations as specified by HAZWOPER 29 CFR 1910.120(a)(1)(i-v) and 1926.65(a)(1)(i-v).
Clean-up at Uncontrolled Hazardous Waste Sites and Clean-up at RCRA Sites
The following hazardous substance clean-up operations within the HAZWOPER standard must comply with all paragraphs of 29 CFR 1910.120 and 29 CFR 1926.65 except paragraphs (p) and (q):
- Clean-up operations that are conducted at uncontrolled hazardous waste sites, required
by a governmental body, whether federal, state, local, or other involving hazardous substances (including but not limited to,
the EPA's National Priority Site List, state priority site lists, sites recommended for the EPA NPL, and initial investigations
of government identified sites which are conducted before the presence or absence of hazardous substances has been ascertained).
[Top]
- Corrective actions involving clean-up operations at sites covered by the Resource
Conservation and Recovery Act of 1976 (RCRA) as amended (42 U.S.C. 6901 et seq.). [Top]
- Voluntary clean-up operations at sites recognized by federal, state, local, or other governmental body as uncontrolled hazardous waste sites. [Top]
Each level triggers a minimum amount of employee training required by their job function, and OSHA specifies topics and training duration. The following job descriptions and typical training time are detailed in 1910.120(e)(3) Initial Training:
General site worker: 40 hours off-site and 24 hours field experience under direct supervision of trained experienced supervisor, includes individuals (such as equipment operators, general laborers and supervisory personnel) engaged in hazardous substance removal or other activities which expose or potentially expose workers to hazardous substances and health hazards. Individuals who use Personal Protective Equipment (PPE) or are exposed to hazards in excess of OSHA’s 8-hour Permissible Exposure Limit (PEL). Employees who may need to respond to a hazardous emergency need a course appropriate to their expected level of response as described below.
Occasional site worker: 24 hours off site and 8 hours field experience under direct supervision of trained experienced supervisor, includes individuals on site only occasionally for a specific limited task (such as, but not limited to, ground water monitoring, land surveying, or geophysical surveying) and who are unlikely to be exposed over permissible exposure limits and published exposure limits.
General site worker where respirators are not necessary: 24 hours off site and 8 hours field experience under direct supervision of trained experienced supervisor, includes individuals regularly on site who work in areas which have been monitored and fully characterized indicating that exposures are under permissible exposure limits and published exposure limits, and the characterization indicates that there are no health hazards or the possibility of an emergency developing.
Management and supervisors: 24 or 40 hours offsite and 8 or 24 hours of supervised field experience in relationship to those supervised. On-site management and supervisors directly responsible for, or who supervise employees engaged in, hazardous waste operations shall receive 40 hours initial training, and three days of supervised field experience (the training may be reduced to 24 hours and one day if the only area of their responsibility is employees that are occasional site workers or general site workers where respirators are not necessary) and at least eight additional hours of specialized training at the time of job assignment on such topics as, but not limited to, the employer's safety and health program and the associated employee training program, personal protective equipment program, spill containment program, and health hazard monitoring procedure and techniques.
Treatment, Storage, and Disposal Facility (TSDF)
The following operations must comply only with the requirements of HAZWOPER standard paragraph (p) of 29 CFR 1910.120 and 29 CFR 1926.65:
- Operations involving hazardous wastes that are conducted at treatment, storage, and disposal facilities regulated by Title 40 CFR Parts 264 and 265 pursuant to RCRA, or by agencies under agreement with EPA to implement RCRA regulations. [Top]
Each level requires a different training program, and OSHA specifies topics and minimum training times. The following job descriptions and typical training time are detailed in 1910.120(p)(7) Training Program and 1910.120(p)(8) Emergency response program:
New employees: 24 hours, for individuals exposed to health hazards or hazardous substances at TSD operations to enable the employees to perform their assigned duties and functions in a safe and healthful manner so as not to endanger themselves or other employees.
Current employees: training equivalent to initial 24 hour training, for employers who can show by an employee's previous work experience and/or training that the employee has had training equivalent to the initial training required. Equivalent training includes the training that existing employees might have already received from actual site work experience.
Emergency response employees at TSD facilities: Training for emergency response employees shall be completed before they are called upon to perform in real emergencies. Such training shall include the elements of the emergency response plan, standard operating procedures the employer has established for the job, the personal protective equipment to be worn and procedures for handling emergency incidents.
- Exception #1: an employer need not train all employees to the degree specified if the employer divides the work
force in a manner such that a sufficient number of employees who have responsibility to control emergencies have the training
specified, and all other employees, who may first respond to an emergency incident, have sufficient awareness training to
recognize that an emergency response situation exists and that they are instructed in that case to summon the fully trained
employees and not attempt control activities for which they are not trained
- Exception #2: An employer need not train all employees to the degree specified if arrangements have been made in advance for an outside fully-trained emergency response team to respond in a reasonable period and all employees, who may come to the incident first, have sufficient awareness training to recognize that an emergency response situation exists and they have been instructed to call the designated outside fully-trained emergency response team for assistance.
Emergency Response Training
- Emergency response operations for releases of, or substantial threats of releases of, hazardous substances without regard to the location of the hazard. Operations within within this scope which are not covered by paragraphs (a)(1)(i) through (a)(1)(iv) of 29 CFR 1910.120 must only comply with the requirements of paragraph (q) of 29 CFR 1910.120. [Top]
Training for employees is required for the health and safety of the workers identifying, responding to, overseeing, and cleaning up release of, or substantial threats of releases of, hazardous substances, including petroleum products, regardless of the location of the hazard.
Each level requires specific training, and OSHA outlines topics and minimum training duration for each. The following job descriptions and typical training time are detailed in 1910.120(q)(6) at www.osha.gov/law-regs.html (note that hours may vary by state requirements):
Train workers to the highest level of responsibility they are assigned.
Not every emergency response worker needs the same amount of training.
Not every emergency response worker needs the same amount of training.
First responder awareness level: no minimum time specified in standard, individuals who are likely to witness or discover a hazardous substance release and who have been trained to initiate an emergency response sequence by notifying proper authorities of the release.
First responder operations level: 8 hours, individuals who provide initial response for the purpose of protecting nearby persons, property, or the environment from the effects of the release and who have been trained to respond in a defensive fashion without actually trying to stop the release.
Hazardous materials technician: 24 hours, individuals who respond for the purposes of stopping the release, approaching the point of release in order to plug, patch or otherwise stop the release.
Hazard materials specialist: 24 hours, individuals who respond with and provide support to the hazardous materials technician for the purposes of stopping the release, approaching the point of release in order to plug, patch or otherwise stop the release. Requires more specific knowledge on the various substances and individuals act as site liaison with Federal, state, tribal government authorities in regard to site activities.
On scene incident commander: 24 hours, will assume control of the incident scene.
For a detailed list of experience and competency levels for each position identified above see Emergency Response Training Requirements
Annual Refresher
Employees and volunteers shall have annual refresher training of sufficient content and duration to maintain their competencies, or shall demonstrate competency in those areas at least yearly. A record of the methodology used to demonstrate competency must be kept by the employer (or the individual if acting as a volunteer). Training can be conducted in segments throughout the year.
Medical Surveillance and Consultation
The following employees shall be incorporated in a medical surveillance program in accordance with HAZWOPER 29 CFR 1910.120(f):
- Employees engaged in clean-up operations conducted at uncontrolled hazardous waste sites and employees of TSDFs,
not covered by exceptions.
- Employees who are or may be exposed to hazardous substances or health hazards at or above the established
permissible exposure limit, above the published exposure levels for these substances, without regard to use of
respirators, for 30 days or more a year.
- All employees who wear a respirator for 30 days or more a year or as required by 1910.134.
- All employees who are injured, become ill or develop signs or symptoms due to possible overexposure involving
hazardous substances or health hazards from an emergency response or hazardous waste operation.
- Members of HAZMAT teams.
Members of an organized and designated HAZMAT team and hazardous materials specialist shall receive a baseline physical examination and be provided with medical surveillance in accordance with HAZWOPER 29 CFR 1910.120(q)(9)
Any emergency response employees who exhibit signs or symptoms which may have resulted from exposure to hazardous substances during the course of an emergency incident either immediately or subsequently, shall be provided with medical consultation in accordance with HAZWOPER 29 CFR 1910.120(f) and in accordance with 1910.120(q)(9).
Exemptions for Evacuation
Facilities that have the potential for an emergency to occur due to an uncontrolled release of hazardous substances or hazardous raw materials are required to provide training required under HAZWOPER 29 CFR 1910.120 paragraph (q). Employers who have hazardous waste storage areas must provide training required under either 29 CFR 1910.120 (p)(8) or (q) for those areas. However, both paragraphs provide exemptions from the basic requirements if the employer intends to evacuate all employees in the event of an emergency and call in a trained emergency response team. In this case employers must provide an emergency action plan and training in accordance with 29 CFR 1910.38(a). The training requirements of 29 CFR 1910.38 are minimal, requiring the training of a sufficient number of persons to assist in the safe and orderly evacuation of employees in the event of an emergency.
Implementing Solutions:
Please submit your experiences (successes/challenges) and tribal-specific documents to share on our website using the attached form.Download Form
Resources:
This 7-page document describes potential areas of overlap between RCRA and Occupational Safety and Health Administration personnel training requirements:RCRA/OSHA Training Requirements [pdf]
FEMA Hazardous Materials Tabletop Exercises Manual [pdf]
Websites:
OSHA Comprehensive Guide to Information Regarding Hazardous Waste Operations:www.osha.gov/SLTC/hazardouswaste/index.html
OSHA Emergency Response Training Requirements are updated and detailed in 29 CFR 1910.120(q)(3) Procedures for handling emergency response:
www.osha.gov/pls/oshaweb/owadisp.show_document?p_table=STANDARDS&p_id=9765
NIEHS Safety and Training of Oil Spill Response Workers provides training tools, courses, presentations, and resources:
http://tools.niehs.nih.gov/wetp/index.cfm?id=2495
NIOSH Respirator Trusted-Source Information Page:
www.cdc.gov/niosh/npptl/topics/respirators/disp_part/RespSource.html
NIOSH Workplace Safety & Health Topics:
www.cdc.gov/niosh/topics/
Oil Spill Prevention and Preparedness Regulations (EPA):
www.epa.gov/oilspill/index.htm
Training Marine Oil Spill Response Workers under OSHA's HAZWOPER Standard:
This informational online booklet is intended to provide a generic, non-exhaustive overview of a particular standards-related topic. This publication does not itself alter or determine compliance responsibilities, which are set forth in OSHA standards themselves and the Occupational Safety and Health Act. Moreover, because interpretations and enforcement policy may change over time, for additional guidance on OSHA compliance requirements, the reader should consult current and administrative interpretations and decisions by the Occupational Safety and Health Review Commission and the Courts:
www.osha.gov/Publications/3172/3172.html
State Occupational Safety and Health Plans:
www.osha.gov/dcsp/osp/index.html
EPA Environmental Response Team:
www.ert.org/
How to use the Emergency Response Guide Video:
www.youtube.com/watch?v=WCpr4Xmhrss
NIOSH Publications Order Forms:
www.cdc.gov/niosh/npg/
NIOSH Data and Statistics Gateway:
www.cdc.gov/niosh/data/
Related Pages:
BrownfieldsContaminated Sites
Federal Facilities
Resource Conservation and Recovery Act
Superfund CERCLA
Underground Storage Tanks
Hazardous Materials Transport
For more information, please contact:
Jennifer Williams, Alaska Program Coordinator, Sr.
Tel: 928/523-0673
Email: Jennifer.Williams@nau.edu
Tel: 928/523-0673
Email: Jennifer.Williams@nau.edu
Last updated: November 21, 2016